Understanding H2S: The Importance of Effective Removal Systems in Industrial Applications
Hydrogen sulfide (H2S) is a colorless gas notorious for its distinctive ‘rotten egg’ odor, its pervasive presence in industrial settings, and its potential health hazards. It naturally emerges from the decay of organic matter and is released during industrial processes, such as refining and wastewater treatment. Managing and removing H2S is beneficial and essential for maintaining a safe work environment and ensuring regulatory compliance. Below, we examine the characteristics of H2S, its impact on health and safety, various methods of removal, and the importance of adhering to regulatory standards.
Traditional and Advanced H2S Removal Techniques
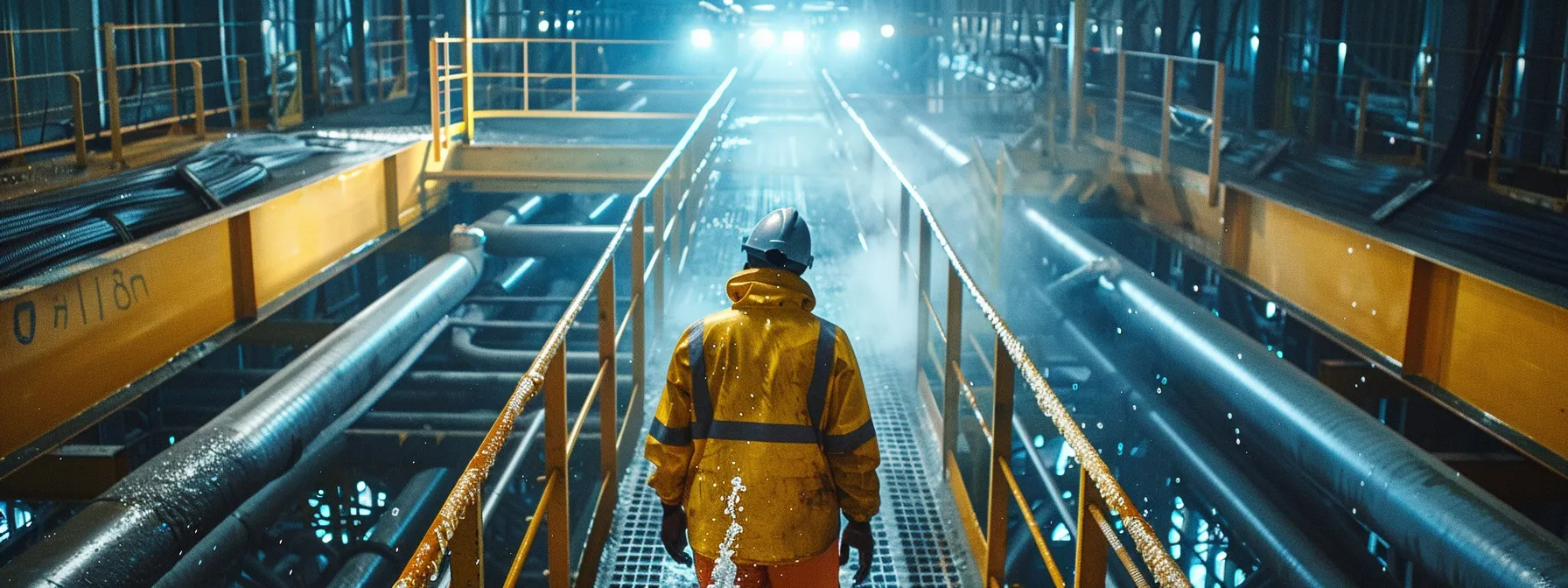
Traditional methods of H2S removal include adsorption, where materials such as activated carbon are used to capture and remove the gas from air streams. Wet scrubbing techniques, which involve dissolving H2S into a liquid medium, are also a standard method. These well-established methods may have limitations, such as high operational costs or the generation of secondary waste products that require further treatment.
Innovations in removal technology have led to the development of more advanced and efficient solutions, including the iron sponge media H2S removal system. This system utilizes a chemical reaction with iron oxide to remove H2S from gas streams, offering a cost-effective and reliable way to address this hazardous issue. These systems continue to evolve with technological advances, providing higher efficiencies and more environmentally friendly solutions.
Other cutting-edge techniques involve biological treatments, where specific microbes are used to convert H2S into harmless end products through biological processes. The adoption of these innovative methods is on the rise, offering industries a more sustainable alternative for H2S mitigation.
Regardless of the chosen method, the primary goal remains reducing H2S levels to safe and acceptable ranges as defined by industry standards. Each facility must consider its unique circumstances, including the volume of H2S and operating conditions, to determine the most effective removal strategy.
How H2S Affects Worker Health and Safety
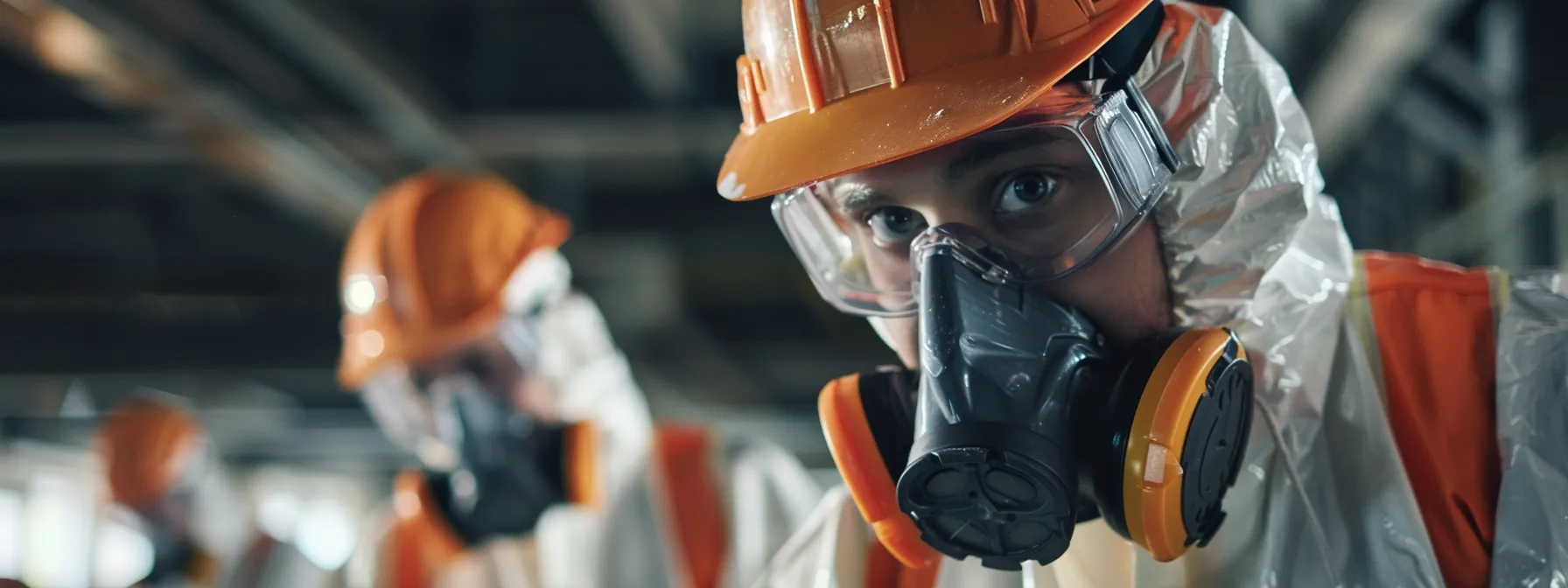
The negative impact of H2S on worker health and safety is a driving factor behind the rigorous industry standards for air quality. Short-term exposure to low levels of H2S can cause headaches, nausea, and eye irritation. Employees are often the first line of defense against these risks, requiring reliable safety protocols and detection systems to prevent prolonged exposure.
As exposure to H2S increases, so does the severity of its health effects. High-level exposure can be life-threatening, causing severe respiratory distress and neurological effects. Employers are responsible for ensuring their workforce is educated on the dangers of H2S and that measures are in place for rapid response and evacuation if necessary.
Moreover, chronic exposure to even small amounts of H2S can result in long-term health problems, including chronic lung disease. These potential outcomes require industries to monitor air quality constantly and have effective H2S removal systems.
Businesses also provide personal protective equipment (PPE), such as gas masks and detectors, to protect workers. This equipment, coupled with regular training on H2S safety procedures, is integral to a comprehensive health and safety program.
Regulatory Standards and Best Practices for H2S Management in Industries
Compliance with regulatory standards is a driving force behind the efforts to manage H2S in industrial settings. Governments and health agencies have established permissible exposure limits (PELs) to dictate the maximum amount of H2S to which workers can be safely exposed. Industries must align their safety protocols and removal system operations with these standards to ensure they are legally compliant and prioritize worker safety.
Best practices in H2S management extend beyond adherence to the regulatory framework. They involve a proactive approach to air quality management, including regular risk assessments, worker training, and the deployment of advanced H2S removal systems. Industries leading the way in H2S management also seek certification in occupational health and safety management systems, like ISO 45001.
Constant review and adaptation are components of best practices, as regulations and technologies are continuously evolving. Companies committed to excellence in H2S management often engage with industry forums and research institutions to stay abreast of changes and refine their practices accordingly.
Perhaps the most crucial best practice is cultivating a safety culture where every worker is aware of and knows the associated risks of H2S. Empowering employees with the proper knowledge and tools ensures they can contribute to a safer work environment and prevent avoidable incidents.
Overall, effectively managing H2S in industrial environments is essential for safeguarding worker health, ensuring operational efficiency, and maintaining regulatory compliance. By adopting advanced removal systems and fostering a proactive safety culture, industries can mitigate risks and promote a safer, more sustainable work environment.